Cylinder Valve Solution for Compress Gases
Compressed gases are stored in high-pressure cylinders, with conditions tailored to the gas’s type, state, and storage environment. For example, gases may be compressed to 104 pounds per square inch at 129.2°F or 40 pounds per square inch at 70°F. To enable safe storage and handling, most cylinders are equipped with at least one valve. This critical component facilitates gas filling, sealing, and releasing while maintaining controlled flow and pressure.
Cylinder valves play a vital role in ensuring safety and efficiency. As the most delicate part of the system, they require careful handling to maximize performance and longevity. Proper knowledge of these valves enhances safety protocols, boosts operational efficiency, and extends equipment lifespan.
This article explores key types of cylinder valves, their applications, operating principles, and best practices for handling them. By understanding these essentials, you can ensure safer and more effective use of compressed gas cylinders.
Types of Compressed Gas Valve
There are four main types of cylinder valves: pressure seal valves, packed valves, O-ring valves, and diaphragm valves, each available in various designs.
High-pressure cylinder valves, such as these, are specifically engineered to withstand the rigorous demands of industries handling compressed gases, ensuring safety, reliability, and optimal performance.
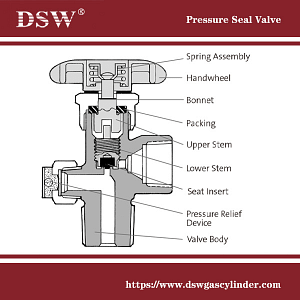
Pressure seal valve
Products: inerts, oxygen, hydrogen
Operating principle: The pressure seal valve is a handwheel-operated valve using a two-piece valve stem.
The upper and lower stems interface with each other.
The threads are located on the lower stem, and the upper limb is free-floating.
A Teflon@ material packing ring that makes contact with a ridge on the upper stem provides the seal around the valve stem.
The force that provides this contact is gas pressure and the spring in the handwheel.
This spring provides upward force to the upper stem and pulls the stem’s sealing ridge into the packing ring.
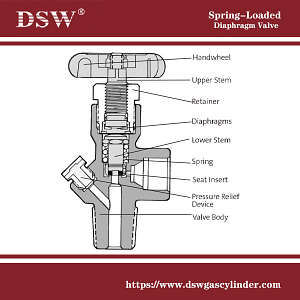
The spring-loaded diaphragm valve
Products: Highly toxic noncorrosive gases, high-purity gases, rare gases, and pyrophoric gases
Operating principle: The diaphragm valve is handwheel‑operated, using a two‑piece stem separated by nonperforated diaphragms. These diaphragms prevent leakage along the valve stem. The lower limb is
encased in a spring, which forces the branch away from the seat when the valve is opened. The upper limb is
threaded into the diaphragm retainer nut. When the handwheel is rotated to the closed position, the upper limb pushes on the diaphragms, which defect downward, forcing the lower limb against the valve seat. When the handwheel is rotated toward the open position, the upper limb is moved away from the diaphragms, allowing the spring to push the lower limb away from the seat. Replacing elastomeric seals with metal diaphragms gives this valve superior leak integrity to the atmosphere.
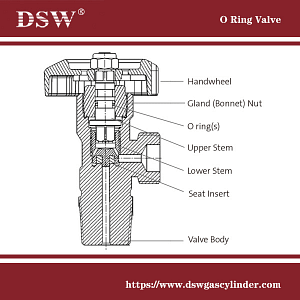
O ring valve
Products: inerts, oxygen, hydrogen
Operating principle: The O ring valve is similar in design to the pressure seal valve, except that O achieves the sealing rings(s) instead of a washer for the upper stem.
They identify features: 1. The design requires no spring, so the handwheel has no wriggle. The handwheel does not rise due to its rotation position, but the user can sense a rise when the valve is initially opened and the gland area is subject to high pressure.
Recommended opening procedure: The valve does not require to be back‑seated during opening.
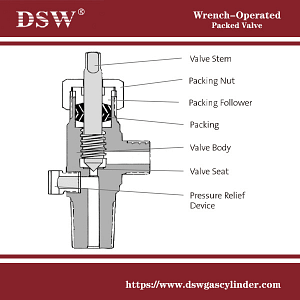
Wrench-Operated Packed Valve
Identifying features
1. This valve does not have a hand wheel. The top of the stem is machined square to accommodate a wrench.
2. The top of the valve has a large, internal‑threaded nut screwed onto the body, where the valve’s stem exits. This is the packing nut.
Recommended opening procedure:
The wrench‑operated valve has a considerable flow capacity. It is unnecessary to open this valve to the fully open position to provide full flow to the Process. Opening this valve entirely poses serious problems. The first problem is safety‑related. In many applications, cylinders with these valves are used in tight quarters (e.g., gas cabinets) or behind barricades. These space constraints often prevent the stem from being fully rotated when the valve operates.
This valve requires approximately three full turns from full open to full close. In the case of an emergency, it can take 15 to 30 seconds to close the valve, depending on
space and operator stress. However, if the valve is opened to the recommended ¼ to ½ turn, the valve can be quickly closed with minimal operator
exposure. The second benefit of only opening the valve the recommended ¼ to ½ turn is the protection of the up-per-section of threads.
Key Considerations for Cylinder Valve Selection
When choosing a valve for your application, consider the following:
- Gas Type: Certain valves are designed for specific gases (e.g., high-purity vs. inert gases).
- Operating Pressure and Temperature: Ensure the valve material and design can withstand the required conditions.
- Application Environment: Evaluate the likelihood of exposure to corrosive elements or confined spaces.
- Maintenance and Repair: Choose valves that are easy to maintain and service and always adhere to the manufacturer’s repair guidelines.
Comparison Chart
Four types of High-Pressure Cylinder Valves highlighting their operating temperature, pressure range, and suitable gases:
This chart helps you compare the key characteristics of each valve type, making it easier to select the right one for your gas storage needs.
Valve Type | Operating Temperature | Pressure Range | Suitable Gases | Key Features |
Pressure Seal Valve | -20°F to 180°F (-29°C to 82°C) | Up to 3,000 psi (207 bar) | Inert gases (e.g., nitrogen), oxygen, hydrogen | Handwheel-operated, Teflon packing for sealing, reliable for high-pressure gases |
Diaphragm Valve | -50°F to 250°F (-46°C to 121°C) | Up to 6,000 psi (414 bar) | Highly toxic, non-corrosive gases; high-purity gases; rare and pyrophoric gases | Superior leak integrity uses metal diaphragms, suitable for critical and hazardous gas applications |
O-Ring Valve | -20°F to 160°F (-29°C to 71°C) | Up to 3,000 psi (207 bar) | Inert gases, oxygen, hydrogen | Compact design uses O-rings for sealing, no spring required, and easy operation. |
Wrench-Operated Packed Valve | -20°F to 180°F (-29°C to 82°C) | Up to 4,500 psi (310 bar) | Industrial gases, including compressed air and inert gases | High flow capacity, requires a wrench for operation, recommended for controlled environments |
Notes:
- Operating Temperature: These ranges can vary depending on specific designs and materials used by manufacturers.
- Pressure Range: Always confirm the valve’s specifications for exact ratings. Some designs may exceed the stated ranges.
- Suitability: Choose the valve based on the gas type, purity level, and required operational integrity.
Applications of Cylinder Valves
Cylinder valves are indispensable in industries like:
- Healthcare: Managing medical gases such as oxygen and nitrous oxide
- Manufacturing: Handling inert or reactive gases for welding and fabrication
- Research Laboratories: Storing high-purity gases for experiments and chemical processes
- Energy: Transporting hydrogen and other gases for renewable energy solutions
Working knowledge of cylinder valves
Working knowledge of cylinder valves can improve processes, save time and money, prevent problems, maintain the valve’s life and integrity, and improve the safety of your operation. This document must not be used as a valve modification or repair guide. No changes to valves are permitted, and any repairs shall only be made by or under the direction of the supplier.
Conclusion
Selecting the correct cylinder valve ensures safe and efficient gas handling. By understanding the operating principles, features, and recommended practices for each valve type, you can optimize your processes, enhance safety, and reduce maintenance costs.
For expert guidance and high-quality cylinder valves, contact us today. Let us help you find the perfect solution for your gas storage needs.
No comment